PCB Thickness: Everything You Need to Know
PCB thickness is a crucial aspect of printed circuit board design and manufacturing that impacts board performance, durability, and compatibility. Understanding the factors that influence PCB thickness and how to choose the right thickness for your application is essential for successful electronics projects.
This comprehensive guide will explore all aspects of PCB thickness, from standard values to design considerations.
Standard PCB Thicknesses
The most common PCB thickness is 1.6 mm (approximately 0.063 inches or 62 mils)1. This standard thickness originated from the early days of PCB manufacturing when 1/16-inch Bakelite sheets were commonly used. While 1.6 mm remains the industry standard, other thicknesses are also widely used:
- 0.8 mm (31 mils)
- 1.0 mm (39 mils)
- 1.6 mm (63 mils)
- 2.36 mm (93 mils)
- 3.17 mm (125 mils)
It’s important to note that these are nominal thicknesses, and actual board thickness may vary due to manufacturing tolerances and other factors.
Factors Affecting PCB Thickness
Several design and manufacturing factors contribute to the overall thickness of a PCB:
1. Number of Layers
The number of layers in a PCB directly impacts its thickness. As the layer count increases, so does the overall board thickness. For example:
- Single-layer PCBs are typically around 1.6 mm thick
- Multi-layer PCBs can be several millimeters thick
2. Copper Weight
Copper weight, measured in ounces per square foot (oz/ft²), affects the thickness of conductive traces on the PCB. Standard copper weights range from 1 oz to 2 oz, but heavier copper can be used for high-current applications. Thicker copper increases overall board thickness.
3. Core and Prepreg Materials
The core (rigid base material) and prepreg (bonding layers) contribute significantly to PCB thickness. For a standard 1.6 mm thick 2-layer PCB, the core material accounts for about 1.5 mm of the total thickness.
4. Solder Mask and Silkscreen
While relatively thin, solder mask and silkscreen layers add to the overall PCB thickness. Typical solder mask thickness is around 0.01 mm per side.
5. Surface Finish
Different surface finishes, such as HASL, ENIG, or immersion silver, can slightly affect the final board thickness.
PCB Thickness Tolerances
Manufacturing tolerances are an important consideration when specifying PCB thickness. Most manufacturers work with a tolerance of ±10% from the nominal thickness. For example, a 1.6 mm board may actually measure between 1.44 mm and 1.76 mm.
Get the PCB Assembly Services at PCBPit.com now >>
Choosing the Right PCB Thickness
Selecting the appropriate PCB thickness depends on various factors:
1. Mechanical Requirements
Thicker boards offer greater mechanical strength and rigidity, which is beneficial for applications subject to vibration or physical stress. Thinner boards are preferred for flexible or space-constrained designs.
2. Thermal Management
Thicker PCBs generally provide better heat dissipation, which is crucial for high-power applications1.
3. Electrical Performance
PCB thickness affects impedance control and signal integrity. Thinner boards may require tighter manufacturing tolerances to maintain consistent impedance.
4. Component Compatibility
Some components, such as edge connectors or specific mounting hardware, may require a particular board thickness.
5. Cost Considerations
Non-standard thicknesses or extremely thick boards may increase manufacturing costs due to specialized materials or processes.
PCB Thickness in Multi-layer Designs
For multi-layer PCBs, thickness considerations become more complex. Designers must account for:
1. Layer Stack-up
The arrangement of copper layers, core materials, and prepreg affects the overall thickness and electrical performance.
2. Impedance Control
Maintaining consistent impedance across layers requires careful consideration of dielectric thicknesses and copper weights.
3. Via Aspect Ratio
As board thickness increases, the aspect ratio (depth to diameter) of vias becomes a critical factor. High aspect ratios can lead to manufacturing challenges and reliability issues.
Manufacturing Considerations
When designing PCBs with specific thickness requirements, keep these manufacturing factors in mind:
1. Material Availability
Standard material thicknesses are more readily available and cost-effective5.
2. Press Cycle
The lamination process can affect the final board thickness, especially for multi-layer designs.
3. Copper Plating
Plated through-holes and vias add copper thickness, which must be accounted for in the overall design3.
4. Surface Finish
Some surface finishes may add more thickness than others, affecting the final board dimensions.
Thickness Measurement and Quality Control
PCB manufacturers typically measure board thickness at multiple points to ensure consistency. Common measurement locations include:
- Corner areas
- Center of the board
- Areas near large copper planes or high-density component regions
Advanced measurement techniques, such as X-ray or ultrasonic scanning, may be used for complex multi-layer boards to verify internal layer thicknesses and detect any delamination issues.
Emerging Trends in PCB Thickness
As electronics continue to evolve, new trends in PCB thickness are emerging:
1. Ultra-thin PCBs
Advancements in materials and manufacturing processes are enabling the production of extremely thin PCBs (less than 0.2 mm) for use in flexible electronics and wearable devices8.
2. High-Density Interconnect (HDI) PCBs
HDI technology allows for thinner overall board profiles while maintaining high layer counts and complex routing.
3. Embedded Components
By integrating components within the PCB layers, designers can reduce overall thickness while increasing functionality.
Conclusion
PCB thickness is a critical design parameter that affects numerous aspects of a board’s performance, manufacturability, and cost. While standard thicknesses like 1.6 mm remain popular, designers have a wide range of options to choose from based on their specific application requirements.
By understanding the factors that influence PCB thickness and working closely with manufacturers, engineers can optimize their designs for both performance and producibility.
FAQs
Q: Can I specify any custom PCB thickness for my design?
A: While many manufacturers offer custom thicknesses, it’s best to stick to standard values when possible. Custom thicknesses may increase costs and lead times. Always consult with your PCB fabricator to determine the feasibility of non-standard thicknesses.
Q: How does PCB thickness affect signal integrity?
A: PCB thickness impacts impedance control and signal propagation. Thicker boards may require wider traces to maintain consistent impedance, while thinner boards can support higher-density routing but may be more susceptible to crosstalk.
Q: Are there any regulatory requirements for PCB thickness in specific industries?
A: Some industries, such as aerospace or medical devices, may have specific requirements or standards for PCB thickness related to reliability and safety. Always check relevant industry standards and regulations when designing PCBs for these applications.
Q: How do I account for PCB thickness variations in my component placement?
A: When designing PCBs, especially for tight-tolerance assemblies, consider the manufacturer’s thickness tolerances. You may need to adjust component placement or use flexible mounting solutions to accommodate potential thickness variations. Consult with your PCB manufacturer and contract manufacturer to ensure your design accounts for realistic tolerances
Share:
More Posts

AllPCB Review: Can We Trust It?
AllPCB Review: Can We Trust It? In this in-depth review, we’ll examine AllPCB’s strengths, weaknesses, and whether it deserves your trust. We’ll also explore PCBPit,

PCBgogo Review: Is It A Good PCB Manufacturer?
PCBgogo Review: Is It A Good PCB Manufacturer? In this in-depth review, we’ll dissect its strengths, weaknesses, and alternatives—with a focus on PCBPit, a rising
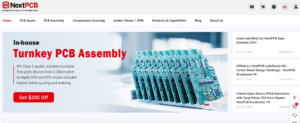
NextPCB Review: Does It Really Work?
NextPCB Review: Does It Really Work? Choosing a reliable PCB manufacturer is critical for bringing your electronics projects to life. NextPCB has been a prominent

OurPCB Review: Is There Any Alternative to This PCB Manufacturer?
OurPCB Review: Find Its Best Alternative Choosing the right PCB manufacturer can make or break your electronics project. Whether you’re a hobbyist building a DIY