A Comparative Study: Aluminum PCB vs. FR4 PCB
Aluminum PCB vs. FR4 PCB
As electronic technology advances relentlessly, the usage of PCBs (Printed Circuit Boards) extends dynamically across its range. Serving as vital parts of electronic devices, PCBs function as the backbone for a variety of applications.
Among all variants, the Aluminum PCB and FR4 PCB (Glass Fiber Reinforced Epoxy Resin PCB) are two predominant types that vary notably in their individual material composition, efficiency, and usability.
A thorough examination of their distinctive traits is essential to demarcate their functionality and specific applications.
Material Composition
Aluminum PCB, as its name suggests, is primarily constructed of aluminum, offering an excellent base for heat conduction. This PCB typically possess an aluminum substrate, layered usually with an insulator to separate the circuit.
In comparison, FR4 PCB incorporates a composite material of glass fiber-reinforced epoxy resin. While this ensures exemplary mechanical strength, its thermal conductivity lags. The prefix “FR” stands for Flame Retardant, denoting its compliance with UL 94V-0 stages.
Heat Conduction Capacity
For applications needing superior thermal conduciveness, Aluminum PCBs are an attractive choice. Their high thermal conduction capacity makes them suitable for applications like LED lighting, which demands efficient heat dispersion as light-emitting components produce a substantial amount of heat.
The Aluminum PCB works optimally to transfer and dissipate this heat, thereby extending the performance and life of the LEDs. On the other hand, due to its primary material being glass fiber-reinforced epoxy resin, FR4 PCB trails behind in thermal conductivity and is less efficient for applications needing potent heat dissipation.
Coefficient of Thermal Expansion
An important factor that could impact the quality of PCB is the coefficient of thermal expansion (CTR). Traditional FR-4 is susceptible to expansion issues affecting the quality of metallized holes and circuit lines.
The sunk copper and the FR-4 board exhibit a considerable difference in CTR – copper’s being 17×10^-6 cm/cm℃ and FR-4’s being 110×10^-6 cm/cm℃. This difference potentializes damage and compromises product reliability.
On the other hand, aluminum substrates have a CTR of 50×10^-6 cm/cm℃, much closer to copper and less than FR-4. This assists in sustaining the quality and reliability of printed circuit boards, making aluminum an apt choice for applications seeking a lower CTR.
Layering Comparison
In terms of layering, the Aluminum PCB houses three exclusive layers, as opposed to the FR4 PCB which can vary from single to multiple layers.
The Aluminum PCB layers comprise the aluminum substrate along with the copper conductive layer and the dielectric layer. This makes Aluminum PCB a better fit for high-temperature settings.
Mechanical Resilience
Aluminum PCB, with its metallic core base, outshines FR4 PCB by offering higher mechanical strength and rigidity. For applications requiring a highly robust PCB to accommodate diverse electrical elements, the Aluminum PCB emerges as a tougher competitor.
Thickness Variance
FR4 PCBs claim superiority over Aluminum PCBs in terms of thickness, with capacity for multi-layer lamination.
Aluminum PCBs lag behind due to limitation by the size of the dielectric or the backing metal layer. The thickest component of an Aluminum PCB, the backing plate, contributes to its additional heat dissipation.
Intended Application
A PCB’s suitability varies based on its intended usage. Aluminum PCBs excel in contexts that demand high thermal and electrical conductivity. They find widespread use in power modules, high-powered RF sectors, automotive electronics to name a few.
FR4 PCBs are preferred in standard electronic circuits and areas that do not necessitate high thermal conduciveness. Their mechanical resilience and electrical insulative properties make them an ideal choice in various common electronic devices. Some specific applications even use the high TG FR4 as they can sustain higher temperatures.
In conclusion, choosing the appropriate PCB type is vital as it directly influences the performance and stability of electronic devices. Aluminum PCBs, being thermally and electrically superior, serve applications requiring these traits. Meanwhile, FR4 PCBs are versatile and fit into most electronic circuits, providing a blend of mechanical strength and insulation. A deep understanding of these differences can aid engineers in making the best decision for particular applications.
In case a variety of thickness in PCBs is required, FR4 PCBs would be the more suitable choice, whereas for applications necessitating robust electromagnetic shielding and heat transferring capabilities, aluminum PCBs are the better call.
Conclusion
The comparative study between Aluminum PCBs and FR4 PCBs underscores the importance of selecting the right materials based on their innate characteristics. It is evident that each type of PCB has its distinct advantages. Aluminum PCBs, with their superior thermal and electrical conductivity, make them an exceptional choice for high-temperature applications and high-powered sectors, while their relatively low Coefficient of Thermal Expansion (CTR) adds to their reliability.
Conversely, FR4 PCBs demonstrate commendable mechanical strength and versatility, catering to a diverse range of electronic circuits. Despite their modest thermal conduciveness, the capacity for multi-layer lamination and impressive electrical insulation properties of FR4 PCBs lend them their importance.
The choice between Aluminum and FR4 PCBs heavily relies on specific application requirements and intricate understanding of their differences. While FR4 PCB might be suitable for a variety of applications and varying thickness requirements, Aluminum PCBs are the preferred choice when the need for robust heat conduction and electromagnetic shielding arises.
In the sphere of PCB manufacturing, companies like PCBPit play a vital role. As a reputed PCB prototype and assembly manufacturer, PCBPit specializes in translating complex circuit board designs into high-performance PCBs, maximizing the functionalities of both Aluminum and FR4 PCBs.
The expert team at PCBPit ensures that each PCB is accomplished flawlessly, regardless of its complexity or quantity. Moreover, they conduct rigorous quality checks, complying with international standards. This not only guarantees optimal functioning but also bolsters reliability. PCBPit further extends its services to PCB design and provides a quick quotation service, fostering a highly efficient and responsive customer service experience.
Importantly, PCBPit has demonstrated laudable commitment to environmentally-friendly practices, providing RoHS compliant PCBs. Thus, for manufacturers seeking a comprehensive solution encompassing intricate PCB design, fabrication and assembly, PCBPit emerges as a sound choice. In essence, an informed decision that factors in both material properties and expert manufacturing practices like those of PCBPit can drastically enhance the performance and longevity of electronic deployments.
Share:
More Posts

AllPCB Review: Can We Trust It?
AllPCB Review: Can We Trust It? In this in-depth review, we’ll examine AllPCB’s strengths, weaknesses, and whether it deserves your trust. We’ll also explore PCBPit,

PCBgogo Review: Is It A Good PCB Manufacturer?
PCBgogo Review: Is It A Good PCB Manufacturer? In this in-depth review, we’ll dissect its strengths, weaknesses, and alternatives—with a focus on PCBPit, a rising
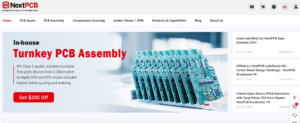
NextPCB Review: Does It Really Work?
NextPCB Review: Does It Really Work? Choosing a reliable PCB manufacturer is critical for bringing your electronics projects to life. NextPCB has been a prominent

OurPCB Review: Is There Any Alternative to This PCB Manufacturer?
OurPCB Review: Find Its Best Alternative Choosing the right PCB manufacturer can make or break your electronics project. Whether you’re a hobbyist building a DIY