SMT Stencil: A Comprehensive Guide
Surface Mount Technology (SMT) has revolutionized the electronics manufacturing industry, enabling the production of smaller, more efficient, and cost-effective printed circuit boards (PCBs). At the heart of this process lies the SMT stencil, a crucial tool that ensures precise and consistent application of solder paste onto PCB pads.
This comprehensive guide will explore the intricacies of SMT stencils, their types, materials, design considerations, and best practices for optimal performance.
What are SMT Stencils?
SMT stencils are thin metal sheets, typically made of stainless steel or nickel alloys, with laser-cut apertures that correspond to the solder pad locations on a PCB. These stencils play a vital role in the SMT assembly process by allowing for the accurate deposition of solder paste, which is essential for creating reliable solder joints between components and the PCB.
Types of SMT Stencils
There are several types of SMT stencils available, each catering to different production needs and requirements:
Framed SMT Stencils
Framed stencils are permanently fixed within a rigid frame, making them ideal for high-volume production. The stencil foil is tightly stretched within the frame, ensuring high-accuracy printing and consistent performance over extended periods. These stencils are particularly well-suited for automated production lines and offer excellent stability during the printing process.
Frameless SMT Stencils
Frameless stencils, also known as foil stencils, are flexible and cost-effective options that are perfect for prototyping and small-scale production. These stencils can be easily stored and are compatible with various stencil tensioning systems. Their flexibility allows for quick design changes and adaptability to different PCB layouts.
Step Stencils
Step stencils feature multiple thickness levels within a single stencil, allowing for optimal solder paste deposition for components with varying pad sizes and requirements. This design is particularly useful when dealing with a mix of fine-pitch and large components on the same PCB.
Get the best pcb manufacturing services at PCBPit >>
Stencil Materials
The choice of stencil material significantly impacts its performance and longevity. Common materials include:
Stainless Steel
Stainless steel is the most widely used material for SMT stencils due to its durability, resistance to corrosion, and excellent print quality. It offers a good balance between cost and performance, making it suitable for a wide range of applications.
Nickel Alloys
Nickel alloys, such as Inconel or Monel, offer superior mechanical strength and high-temperature resistance. These materials are particularly beneficial in demanding environments or applications requiring extended stencil life.
Stencil Manufacturing Processes
The precision and quality of SMT stencils depend largely on the manufacturing process used. The two primary methods are:
Laser Cutting
Laser cutting is the most common and precise method for creating stencil apertures. High-powered lasers are used to cut the desired aperture shapes and sizes into the stencil material, offering excellent accuracy and repeatability. This method is ideal for creating fine-pitch apertures and complex designs.
Chemical Etching
Chemical etching is an alternative process that involves using a photoresist mask and chemical solution to create apertures. While less precise than laser cutting, it can be cost-effective for larger apertures or thicker stencils.
Design Considerations for SMT Stencils
Proper stencil design is crucial for achieving high-quality solder paste prints and minimizing defects. Key factors to consider include:
Aperture Size and Shape
The size and shape of stencil apertures should match the PCB pads while accounting for the solder paste’s properties and desired solder joint profile. Common aperture shapes include rectangles, circles, and home plates. Designers must adhere to minimum aperture width and pitch guidelines to ensure proper paste release and prevent bridging.
Stencil Thickness
Selecting the appropriate stencil thickness is critical for achieving optimal solder paste volume and print quality. Thinner stencils are ideal for fine-pitch components but may struggle with sufficient paste volume, while thicker stencils can provide robust deposits but may hinder paste release. Manufacturers must balance thickness based on PCB design, component specifications, and solder paste characteristics.
Area Ratio
The area ratio, which is the ratio of aperture opening area to its wall area, is a crucial factor in determining paste release efficiency. A higher area ratio generally results in better paste release. For optimal performance, designers should aim for an area ratio of 0.66 or higher.
Aspect Ratio
The aspect ratio, defined as the width of the aperture divided by the stencil thickness, also affects paste release. A minimum aspect ratio of . is recommended to ensure proper paste transfer and prevent clogging of apertures.
Stencil Maintenance and Cleaning
Proper maintenance and cleaning of SMT stencils are essential for ensuring consistent print quality and extending the stencil’s lifespan. Best practices include:
Regular Cleaning
Implement a regular cleaning schedule to remove solder paste residue and prevent aperture clogging. Cleaning methods may include manual wiping with solvents, ultrasonic cleaning, or automated stencil cleaning systems.
Inspection
Regularly inspect stencils for damage, wear, or aperture clogging to maintain print quality. Use magnification tools to examine apertures for any signs of deformation or blockage.
Proper Storage
Store stencils in a clean, dry environment and use protective covers to prevent damage during handling and transportation. Proper storage helps maintain the stencil’s integrity and prolongs its useful life.
Optimizing Stencil Performance
To achieve the best results with SMT stencils, consider the following optimization techniques:
Nano-coating
Applying a nano-coating to the stencil surface can improve paste release and reduce the need for frequent cleaning. This treatment enhances the stencil’s hydrophobic properties, making it easier for solder paste to separate from the aperture walls.
Electropolishing
Electropolishing the stencil surface can smooth out microscopic imperfections, improving paste release and print quality. This process can be particularly beneficial for fine-pitch applications where consistent paste deposition is critical.
Custom Aperture Designs
For challenging components or unique PCB layouts, custom aperture designs can be implemented to optimize paste deposition. This may include modified shapes, stepped apertures, or specialized patterns to address specific printing requirements.
Future Trends in SMT Stencil Technology
As electronics continue to evolve, SMT stencil technology is also advancing to meet new challenges:
D-Printed Stencils
Additive manufacturing techniques are being explored for creating complex, multi-level stencils that can accommodate a wide range of component types and sizes on a single PCB.
Smart Stencils
Integration of sensors and data collection capabilities into stencils could provide real-time feedback on print quality and stencil performance, enabling proactive maintenance and process optimization.
Advanced Materials
Research into new stencil materials with enhanced properties, such as improved wear resistance or self-cleaning capabilities, could further improve stencil performance and longevity.
Conclusion
SMT stencils are indispensable tools in modern electronics manufacturing, enabling precise and efficient solder paste application. By understanding the various types, materials, design considerations, and best practices associated with SMT stencils, manufacturers can optimize their PCB assembly processes and produce high-quality electronic products. As technology continues to advance, SMT stencil innovations will play a crucial role in meeting the demands of increasingly complex and miniaturized electronic designs.
FAQs
1. What is the optimal thickness for an SMT stencil?
The optimal thickness for an SMT stencil typically ranges from 0. mm to 0. mm (-8 mils). However, the ideal thickness depends on factors such as component size, pad dimensions, and solder paste properties. Fine-pitch components may require thinner stencils, while larger components might benefit from thicker stencils.
2. How often should I clean my SMT stencil?
The frequency of cleaning depends on factors such as production volume, solder paste properties, and environmental conditions. As a general rule, clean the stencil after every -0 prints or when you observe a decline in print quality. Implement a regular cleaning schedule and adjust based on your specific production needs.
3. Can I reuse an SMT stencil for different PCB designs?
While it’s possible to reuse stencils for similar PCB designs, it’s generally not recommended to use a single stencil for significantly different layouts. Each PCB design typically requires a custom stencil to ensure optimal solder paste deposition. However, for small production runs or prototyping, universal stencils with adjustable apertures are available.
4. What are the signs that my SMT stencil needs replacement?
Signs that your SMT stencil may need replacement include:Visible wear or damage to apertures
Share:
More Posts

AllPCB Review: Can We Trust It?
AllPCB Review: Can We Trust It? In this in-depth review, we’ll examine AllPCB’s strengths, weaknesses, and whether it deserves your trust. We’ll also explore PCBPit,

PCBgogo Review: Is It A Good PCB Manufacturer?
PCBgogo Review: Is It A Good PCB Manufacturer? In this in-depth review, we’ll dissect its strengths, weaknesses, and alternatives—with a focus on PCBPit, a rising
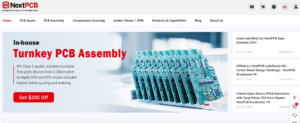
NextPCB Review: Does It Really Work?
NextPCB Review: Does It Really Work? Choosing a reliable PCB manufacturer is critical for bringing your electronics projects to life. NextPCB has been a prominent

OurPCB Review: Is There Any Alternative to This PCB Manufacturer?
OurPCB Review: Find Its Best Alternative Choosing the right PCB manufacturer can make or break your electronics project. Whether you’re a hobbyist building a DIY