Understanding the Differences Among Rigid, Flex, and Rigid-Flex PCBs
What Are the Differences Among Rigid, Flex, and Rigid-Flex PCBs?
The fundamental difference between a rigid PCB and a flexible PCB is their base layer or substrate, with rigid PCBs built on a non-bendable substrate and flexible PCBs using a flexible base material, allowing for bending and twisting.
Both types serve to conduct electrical current and link electronic components, with rigid PCBs offering strength and flexible PCBs providing durability in flexibility. Additionally, the rigid-flex PCB combines the features of both to maximize functional efficiency and broaden the capabilities of various applications.
Rigid PCBs vs. Flex PCBs: Key Contrasts
While both types of PCB fulfill the function of connecting electronic components, they differ significantly in their manufacturing, performance, and properties:
- Base Layer: Rigid boards employ a non-conductive substrate with conductive tracks, typically containing glass for strength, while flex PCBs use a flexible base material such as polyimide.
- Flexibility: Rigid PCBs are rigid and sturdy due to their base material, while flexible PCBs allow for bending and folding to suit diverse applications.
- Conductors: Rigid circuits use electro-deposited copper, whereas flexible circuits may opt for more flexible rolled annealed copper to accommodate bending.
- Manufacturing Process: Rigid boards use solder mask applications, whereas flexible PCBs use overlay or coverlay processes to protect exposed circuitry.
- Cost: Flex circuits are pricier than rigid ones, but their ability to fit into compact spaces drives demand in various industries, leading to more revenue and indirect savings for manufacturers.
- Durability: Rigid PCBs offer higher strength, while flexible PCBs better absorb vibrations, dissipate heat, and withstand environmental elements. The latter can also be flexed repeatedly without failure.
- Weight: Rigid PCBs are slightly heavier than flexible PCBs due to their strength and thickness, offering potential benefits for creating lightweight electronic devices.
- Resistance: Flexible PCBs exhibit high resistance to extreme environments and temperatures, while rigid PCBs are more susceptible to damage from heat, radiation, or chemicals.
- Design Sophistication: Flexible PCBs are ideal for complex products due to their advanced design, while rigid PCBs are suitable for more basic consumer devices such as toys and musical keyboards.
Understanding Rigid-Flex PCBs
Rigid-flex PCBs leverage a combination of rigid and flexible board technologies, incorporating layers of flexible circuit substrates attached to rigid boards. Typically, these boards are produced with flexible polyimide material on copper cladding substrate, offering enhanced reliability, performance, and flexibility for electronic devices.
Advantages
Rigid-flex PCBs are praised for their lightweight nature, ease of assembly and repair, and their ability to enhance the reliability and performance of electronic devices, especially in compact and innovative designs. Furthermore, their adaptability to smaller devices and miniature components makes them an attractive choice for modern electronic devices.
Benefits of Rigid-Flex PCBs
Enhanced Reliability
By reducing solder joints and board-to-board connectors, rigid-flex PCBs minimize the risk of connection impedance, leading to more secure and reliable connections between attached rigid and flexible layers. This results in fewer circuit failures, enhancing overall reliability.
Efficient Use of Space
The integrated flexible substrate of rigid-flex PCBs provides more space on the board to route traces, making them ideal for compact designs that have limited room for wire harnesses and high-profile connectors.
Cost Savings
While rigid-flex PCBs may be initially more expensive than standard rigid PCBs, they offer cost-effectiveness in terms of assembly charges. The reduction in material and connections required for assembly lowers overall manufacturing costs and increases revenue.
Simplified Testing
The interconnected subcircuits of rigid-flex PCBs facilitate automated testing, enabling manufacturers to identify and eliminate connectivity issues before final component assembly, thus reducing wastage and expenses.
Design Flexibility
With the ability to fit into small devices and a remarkable bend radius, rigid-flex PCBs offer significant design flexibility, unlike rigid boards, allowing for diverse applications.
Resistance to Harsh Conditions
Utilizing materials with high thermal stability, rigid-flex PCBs can withstand high temperatures and are resistant to radiation, oils, chemicals, shocks, vibrations, and other harsh industrial conditions, making them suitable for demanding environments.
Disadvantages of Rigid-Flex PCBs
Despite the advantages, rigid-flex PCBs have drawbacks, including lengthy and complex production processes, challenges in design adjustments during testing, and a relatively low yield rate, which manufacturers carefully consider.
Applications of Rigid-Flex PCBs
Rigid-flex PCBs are widely utilized in various industries, including medical, aerospace, telecommunications, consumer appliances, automotive, military, and manufacturing, due to their unique characteristics and functional benefits.
Conclusion
The development of rigid-flex PCBs has significantly impacted electronic device design and manufacturing, offering a combination of properties and functions that make them relevant for diverse applications. You can always find PCBPit for PCB manufacturing services.
Share:
More Posts

AllPCB Review: Can We Trust It?
AllPCB Review: Can We Trust It? In this in-depth review, we’ll examine AllPCB’s strengths, weaknesses, and whether it deserves your trust. We’ll also explore PCBPit,

PCBgogo Review: Is It A Good PCB Manufacturer?
PCBgogo Review: Is It A Good PCB Manufacturer? In this in-depth review, we’ll dissect its strengths, weaknesses, and alternatives—with a focus on PCBPit, a rising
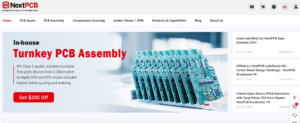
NextPCB Review: Does It Really Work?
NextPCB Review: Does It Really Work? Choosing a reliable PCB manufacturer is critical for bringing your electronics projects to life. NextPCB has been a prominent

OurPCB Review: Is There Any Alternative to This PCB Manufacturer?
OurPCB Review: Find Its Best Alternative Choosing the right PCB manufacturer can make or break your electronics project. Whether you’re a hobbyist building a DIY