Why are Printed Circuit Boards Green?
Printed Circuit Boards (PCBs) are the unsung heroes of the modern electronics industry. They play a vital role in almost every electronic device we use today, from smartphones to laptops, and even the most complex supercomputers. But have you ever wondered why PCBs are typically green in color?
It’s a question that might have crossed your mind as you disassembled a broken gadget or marveled at the inner workings of your favorite electronic device. In this article, we’ll delve into the reasons behind the green hue of PCBs and explore the fascinating history, materials, and environmental aspects associated with them.
The Origin of the Green PCB
The Early Days of PCBs
To understand why PCBs are predominantly green, we need to take a trip back in time to the early days of electronics. Before PCBs, electronic circuits were constructed using point-to-point wiring on terminal strips or breadboards. This method was labor-intensive and not suitable for mass production. As technology advanced, the need for a more efficient and cost-effective solution became apparent.
In the mid-20th century, engineers and innovators began experimenting with various materials and designs for creating a better electrical interconnection system. One of the breakthroughs was the development of the PCB, which streamlined the assembly of electronic components. These early PCBs were not green; they were typically made from materials like paper phenolic or fiberglass, and their color depended on the substrate used.
The Adoption of the Green Color
The green color of PCBs can be attributed to the material known as solder mask. Solder mask is a thin protective layer applied to the surface of the PCB to insulate the conductive copper traces and prevent short circuits. The most common material used for solder mask is a thermosetting epoxy resin with pigments added for coloration.
Historically, the pigments used for solder mask were green because they offered several advantages.
Advantages of the Green Color
Visibility and Clarity
The primary reason for using green solder mask was its excellent visibility and contrast. The bright green color provided a high level of contrast against the copper traces, making it easier for assembly line workers and technicians to inspect the PCB for defects and soldering errors. This enhanced visibility greatly improved the quality control process, reducing the likelihood of manufacturing defects and ensuring better reliability for electronic products.
Tradition and Familiarity
Once the green solder mask became the industry standard, it created a sense of tradition and familiarity. Engineers, designers, and manufacturers became accustomed to the green PCBs, and this consistency helped streamline the design and production process.
Over time, green PCBs became an integral part of the electronics landscape, further cementing their status as the default choice.
Modern PCB Colors
While green PCBs continue to be the most common choice in the industry, they are by no means the only option available today. The development of advanced solder mask materials and technologies has expanded the color palette for PCBs.
Depending on the manufacturer and the specific requirements of a project, PCBs can now be found in a variety of colors, including blue, red, black, and even white.
Customization and Branding
The ability to choose from a range of colors has opened up new possibilities for customization and branding in the electronics industry. Manufacturers can opt for colored PCBs to match the aesthetic design of their products or to make their devices stand out in a crowded market. This level of customization not only enhances the visual appeal of electronic devices but also reinforces brand identity.
UV LED Curing
One of the key advancements in solder mask technology that has enabled a broader spectrum of colors is UV LED curing. Traditional solder mask curing methods involved thermal processes, which limited the range of pigments that could be used.
UV LED curing, on the other hand, allows for the use of a wider variety of pigments and facilitates the creation of colorful and highly durable solder masks.
Environmental Considerations
RoHS Compliance
In addition to aesthetics and functionality, the color of PCBs can also have implications for environmental compliance. The electronics industry has seen a growing emphasis on sustainability and environmental responsibility.
The Restriction of Hazardous Substances (RoHS) Directive, for instance, restricts the use of certain hazardous materials in electronic products. Manufacturers must ensure their PCBs comply with these regulations, regardless of their color.
Green and Sustainable Choices
Interestingly, the green color of PCBs aligns with the broader goals of sustainability. Green solder mask materials are often chosen not only for their visibility but also for their environmentally friendly properties.
Many green solder mask formulations are free from harmful substances and are more easily recyclable than some alternative colors. As a result, green PCBs continue to be a responsible and sustainable choice for electronics manufacturers.
Conclusion
In the world of electronics, the green color of Printed Circuit Boards serves as a symbol of tradition, functionality, and environmental responsibility. While other colors have made their way into the PCB landscape, green remains the industry standard due to its visibility, contrast, and familiarity. However, the ability to choose from a wider range of colors, thanks to advancements in solder mask technology, has given manufacturers the option to tailor their PCBs to meet specific design and branding needs.
As we look ahead to the future of electronics, it’s worth considering the role of PCBs not only as functional components but also as symbolic artifacts. They represent the evolution of technology and the ongoing pursuit of innovation and sustainability.
The next time you open up a device or catch a glimpse of the inner workings of your favorite electronic gadget, take a moment to appreciate the green PCBs that make it all possible. And remember that behind that humble green exterior lies a world of engineering marvels and environmental consciousness that continue to shape our digital lives.
Share:
More Posts

AllPCB Review: Can We Trust It?
AllPCB Review: Can We Trust It? In this in-depth review, we’ll examine AllPCB’s strengths, weaknesses, and whether it deserves your trust. We’ll also explore PCBPit,

PCBgogo Review: Is It A Good PCB Manufacturer?
PCBgogo Review: Is It A Good PCB Manufacturer? In this in-depth review, we’ll dissect its strengths, weaknesses, and alternatives—with a focus on PCBPit, a rising
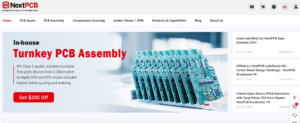
NextPCB Review: Does It Really Work?
NextPCB Review: Does It Really Work? Choosing a reliable PCB manufacturer is critical for bringing your electronics projects to life. NextPCB has been a prominent

OurPCB Review: Is There Any Alternative to This PCB Manufacturer?
OurPCB Review: Find Its Best Alternative Choosing the right PCB manufacturer can make or break your electronics project. Whether you’re a hobbyist building a DIY