ASA vs ABS: Understand the Main Differences
When it comes to choosing materials for manufacturing, engineering, or DIY projects, thermoplastics like ASA and ABS are popular options. Both are widely used in industries ranging from automotive to consumer goods, but they have distinct properties that make them suitable for different applications.
If you’ve ever wondered which material is right for your project, this article breaks down their key differences in simple terms.
By the end, you’ll understand how their chemical makeup, weather resistance, strength, cost, and other factors influence their real-world performance. Let’s dive in!
What is ABS?
ABS (Acrylonitrile Butadiene Styrene) is a common thermoplastic polymer known for its toughness, affordability, and versatility. It’s made by combining three monomers:
- Acrylonitrile: Adds chemical and heat resistance.
- Butadiene: Provides durability and impact strength.
- Styrene: Contributes rigidity and makes the material easy to process.
This blend gives ABS a balance of strength, flexibility, and moldability. You’ll find ABS in everyday items like LEGO bricks, keyboard keys, automotive trim, and protective housings for power tools.
Key Advantages of ABS:
- High impact resistance, even at low temperatures.
- Lightweight and easy to machine or mold.
- Cost-effective compared to many engineering plastics.
Limitations of ABS:
- Poor UV resistance: Prolonged sun exposure causes fading, brittleness, and cracking.
- Moderate heat resistance: It warps or softens at temperatures above 80°C (176°F).
- Susceptible to solvents: Can dissolve or degrade when exposed to acetone or strong acids.
ABS is a go-to material for indoor applications where UV exposure and extreme temperatures aren’t concerns.
What is ASA?
ASA (Acrylonitrile Styrene Acrylate) is often called the “weather-resistant cousin” of ABS. Its chemical structure replaces ABS’s butadiene (the “B” in ABS) with an acrylic ester. This small change significantly improves its performance in outdoor environments.
Key Advantages of ASA:
- Superior UV and weather resistance: Retains color and strength even after years outdoors.
- Good impact resistance: Not quite as tough as ABS but still durable.
- Heat stability: Performs better than ABS at higher temperatures.
- Aesthetic appeal: Resists yellowing and maintains a smooth surface finish.
Limitations of ASA:
- Higher cost: More expensive than ABS due to specialized additives.
- Slightly lower impact strength: Less ideal for high-stress indoor applications.
ASA is commonly used for outdoor products like garden equipment, automotive exterior parts, and electrical enclosures exposed to sunlight.
Try PCB Manufacturing Services at PCBPit >>
Key Differences Between ASA and ABS
To decide which material suits your needs, let’s compare their properties side by side.
1. Chemical Composition
- ABS: Combines acrylonitrile, butadiene, and styrene. Butadiene (a rubbery component) boosts toughness but is vulnerable to UV degradation.
- ASA: Swaps butadiene for an acrylic ester. This acrylic layer shields the material from sunlight and oxidation.
Takeaway: ASA’s acrylic component makes it inherently weatherproof, while ABS prioritizes impact resistance.
2. Weather Resistance
- ABS: Degrades quickly outdoors. UV rays break down butadiene, causing fading, brittleness, and cracks.
- ASA: UV stabilizers and acrylic esters prevent degradation. ASA lasts years outdoors without significant wear.
Example: An ABS garden chair might crack after one summer, while an ASA version remains intact for seasons.
3. Mechanical Properties
- Impact Resistance: ABS wins here, especially in cold environments. Its butadiene absorbs shocks effectively.
- Tensile Strength: Both have similar rigidity (~40–50 MPa), but ASA is slightly more flexible.
Use Case: ABS is better for protective gear; ASA suits outdoor fixtures needing moderate flexibility.
4. Thermal Resistance
Both soften around 90–100°C, but ASA handles sustained heat slightly better. ABS becomes brittle faster when exposed to temperature fluctuations.
Example: ASA is preferred for car mirror housings, which face both heat and UV exposure.
5. Cost
- ABS: Cheaper and widely available (~
- 2–
- 2–3 per kilogram).
- ASA: Costs 20–50% more due to acrylic esters and UV additives.
Tip: For budget-friendly indoor projects, ABS is often the better choice.
6. Processing
Both can be injection-molded, extruded, or 3D-printed. However:
- ABS: Easier to process but emits fumes when melted (ventilation is essential).
- ASA: Requires higher printing temperatures but warps less than ABS during cooling.
7. Aesthetic Qualities
- ABS: Prone to discoloration and surface flaws over time.
- ASA: Retains color vibrancy and gloss, even after prolonged sun exposure.
Ideal For: ASA is popular in automotive exteriors and signage where appearance matters.
8. Chemical Resistance
- ABS: Vulnerable to oils, acids, and solvents.
- ASA: Slightly better resistance to environmental chemicals (e.g., pollution, rainwater).
Applications: Where Are ASA and ABS Used?
Common Uses of ABS
- Toys (e.g., LEGO, action figures).
- Automotive interiors (dashboards, trim).
- Consumer electronics (keyboards, printer housings).
- Protective gear (helmets, luggage cases).
Common Uses of ASA
- Outdoor equipment (lawnmower panels, garden furniture).
- Automotive exteriors (mirror housings, bumper trims).
- Construction (roofing, window frames).
- Electrical enclosures (outdoor junction boxes).
Choosing Between ASA and ABS
Consider these factors when picking a material:
- Environment: Outdoor or high-UV? Choose ASA. Indoor? ABS saves money.
- Mechanical Stress: For impact-heavy uses (e.g., tool handles), ABS is better.
- Budget: ABS is more economical for large-scale production.
- Aesthetics: ASA maintains color and finish longer.
Hybrid Solutions: Some manufacturers blend ASA and ABS to balance cost and weather resistance.
Conclusion
ASA and ABS are both versatile thermoplastics, but their differences are critical for long-term performance. ABS excels in impact resistance and affordability, making it ideal for indoor products. ASA, while pricier, offers unmatched durability for outdoor applications. By understanding their strengths and limitations, you can select the right material to ensure your project’s success—whether it’s a child’s toy or a rooftop solar panel casing.
Next time you’re designing a product, ask yourself: Will this face sun, rain, or physical stress? The answer will guide you to ASA, ABS, or a smart combination of both.
Share:
More Posts
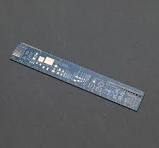
PCB Ruler: A Comprehensive Guide
PCB Ruler: A Comprehensive Guide What is a PCB Ruler? A PCB ruler is a functional tool made from the same materials as a printed
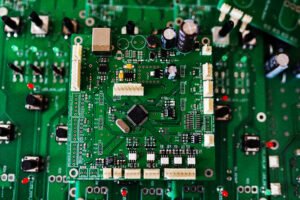
Thermal Vias: A Comprehensive Guide for PCB Heat Management
Thermal Vias: A Comprehensive Guide for PCB Heat Management Why Heat Management Matters in PCBs Before diving into thermal vias, let’s understand why heat is

PCB Testing Guide: Everything You Need to Know
PCB Testing Guide: Everything You Need to Know This guide will walk you through the essentials of PCB testing, including why it matters, common testing
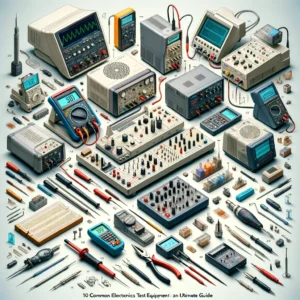
What Is A Rogers PCB?
What Is A Rogers PCB? If you’ve ever used a smartphone, connected to Wi-Fi, or marveled at satellite communication, you’ve indirectly interacted with a technology