What Are PCB Stiffeners?
PCB stiffeners act as additional components applied to circuit boards, which aren’t part of the core PCB design. They play vital roles in bolstering particular regions of the PCB and streamlining the board's handling process.
Stiffeners bolster the robustness of PCBs to combat various operational and manufacturing difficulties. In instances involving flexible PCBs, to achieve a state of rigidity in specific sectors, mechanical support, known as PCB stiffeners, is integrated.
Benefits of Employing PCB Stiffeners
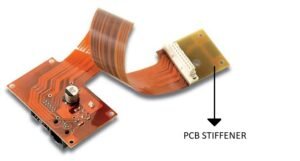
- Mechanical Reinforcement: Stiffeners improve the rigidity and structural fortitude of targeted PCB zones, mitigating warping, flexing, and contortion, which is crucial for weight-bearing sections or high-stress situations.
- Resistance to Flexing: They play a key role in counteracting flexural stress, upholding the circuit board’s stability and operational dependability, which is essential to avert harm to flexible PCBs during the processes of installation, handling, or normal operation.
- Improved Heat Dissipation: Stiffeners contribute to effective heat distribution and dissipation, which fosters superior thermal control on the PCB and circumvents overheating and thermal inconsistency.
- Reinforcement of Connection Sites: Strategic application of stiffeners reinforces connectors, ports, and breakable circuit elements, shielding them from potential wear and tear during connection, disconnection, or regular activity.
- Mounting Auxiliary Components: Stiffeners create a conducive environment for affixing supplementary components like heat sinks, sensors, or electronic modules, thus expanding the circuit board’s functionalities.
- Alignment Accuracy: They also act as guiding fixtures for correct positioning of the circuit board during the assembly process, which serves to minimize assembly errors.
- Dampening Vibration and Resonance: The addition of stiffeners is instrumental in dampening circuit board vibrations and resonances, enhancing signal integrity and reducing interference.
In essence, PCB stiffeners are indispensable for fortifying the performance and dependability of flexible circuit boards, particularly in applications demanding augmented mechanical strength and stability in designated sections.
Click to get PCB Assembly services at PCBPit >>
Varieties of PCB Stiffeners
Understanding the available varieties of PCB stiffeners is critical for selecting the suitable kind for your flexible PCB venture. The following outlines some of the stiffener types:
Polyimide (PI) Stiffeners
Comprising a high-temperature-tolerant polymer film, polyimide stiffeners—stackable for increased thickness—are popular choices due to their solder resistance and strong adhesive qualities. These stiffeners are applied to create controlled bending points and contact tolerances during the assembly process.
In particular, they hinder flexibility in select PCB areas earmarked for integration into a final product. They find use where gold finger insertion slots are present or on opposite sides, enhancing wear resistance.
Kapton, a widely utilized form of polyimide, is preferable for its role in augmenting the flexibility of a PCB’s extremities and enabling the attachment of components like ZIF connectors. In these scenarios, Kapton provides necessary support, thus ensuring the PCB operates effectively and reliably.
FR-4 Stiffeners
With its basis in a glass fiber laminate interwoven with epoxy resin, FR-4 is the go-to material for many stiffeners in flexible circuits. FR-4 imparts a rigid backing for the flex PCB during component placement and thermal reflow.
The integration of an FR-4 border to the PCB perimeters can replace SMT carriers and curtail costs during the assembly, as it allows PTH components to directly access solder pads.
Metal Stiffeners (Stainless Steel or Aluminum)
For designs demanding exceptional formability, corrosion resistance, and long-term durability, stiffeners made from stainless steel or aluminum are top-notch choices. These enhance the assembly process by providing the flexible PCB with additional sturdiness.
Check PCBPit for all-in-one PCB solutions >>
Stiffener Placement in Flexible PCBs
Top Layer Stiffeners
Stiffeners upon the upper surface of flexible PCBs are designated for providing overall structural support. They are especially required when the flexible PCB is tasked with managing substantial loads, such as when connecting to heavy instruments like LED screens, aiding in load distribution across the PCB’s surfaces.
Bottom Layer Stiffeners
When particular regions of a flexible PCB call for extra reinforcement—possibly areas laden with active components—bottom layer stiffeners are applied there to bolster mechanical support while also mitigating the risk of repetitive stress damage.
Dual Layer Stiffeners (Top and Bottom)
Utilizing stiffeners on both the top and bottom layers results in significantly increased stability and rigidity of the flexible PCB, typically situated at pivotal board sections. These may be comprised of various substances, such as different metals and polymers. When planning a design with multiple stiffeners, it’s important to distinguish which flex PCB zones require more rigidity. This could be identified through mechanical area assessments or by pinpointing likely flex spots in the final product.
Occasionally, infusing stiffeners on both the top and bottom layers is necessary for bolstering the flexible PCB’s structural integrity comprehensively. Applications requiring multidirectional bending or compression resistance can benefit from this approach. Intensely dynamic environments might necessitate increased rigidity in several directions, and thus the dual-layer placement offers additional design malleability to comply with complex requirements.
Methods of Attaching Stiffeners to a Flexible PCB
Two primary techniques exist for affixing PCB stiffeners to a flexible PCB, namely Thermal Bonding and Pressure-sensitive Adhesive (PSA).
Each option brings its own set of pros and cons to the table, and the ultimate selection should align with specific design goals, environmental demands, and material considerations. Thermal bonding ensures a more robust mechanical bond, fitting for high-stress applications, though it may necessitate advanced equipment. PSA, while simpler and more economical, might lack long-term stability in certain conditions and is better suited to lighter-stress applications or those requiring removability.
Share:
More Posts

AllPCB Review: Can We Trust It?
AllPCB Review: Can We Trust It? In this in-depth review, we’ll examine AllPCB’s strengths, weaknesses, and whether it deserves your trust. We’ll also explore PCBPit,

PCBgogo Review: Is It A Good PCB Manufacturer?
PCBgogo Review: Is It A Good PCB Manufacturer? In this in-depth review, we’ll dissect its strengths, weaknesses, and alternatives—with a focus on PCBPit, a rising
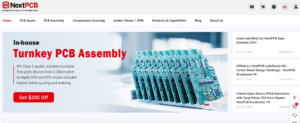
NextPCB Review: Does It Really Work?
NextPCB Review: Does It Really Work? Choosing a reliable PCB manufacturer is critical for bringing your electronics projects to life. NextPCB has been a prominent

OurPCB Review: Is There Any Alternative to This PCB Manufacturer?
OurPCB Review: Find Its Best Alternative Choosing the right PCB manufacturer can make or break your electronics project. Whether you’re a hobbyist building a DIY